Rotary hammer purchasing advice: how to choose the right product
- The most important facts in brief
- A hammer drill is a tool that can be used to work on very hard rock or concrete. The main functions are drilling holes and chiseling.
- Electric hammer drills are best suited for home and handymen. Their power is sufficient for most work in these areas.
- You can tell how powerful a hammer drill is by its impact strength in joules, the number of blows and the motor power in watts.
- Hammer drills usually use a special insertion system for attachments called SDS.
- With an interchangeable drill chuck or a drill chuck adapter, you can also use ordinary drill bits with a smooth shank.
When the going gets tough
For hard materials, a simple drill or percussion drill is often not enough. They also sometimes reach their limits with thick house walls in old or new flats: Drilling a hole in the wall to fix a shelf, for example, becomes a test of patience. With a hammer drill, you can easily master this task: it specialises in working hard rock and concrete. The largest and most powerful models are therefore found in mining applications, among others. But also do-it-yourselfers will find the right tool in the wide range.
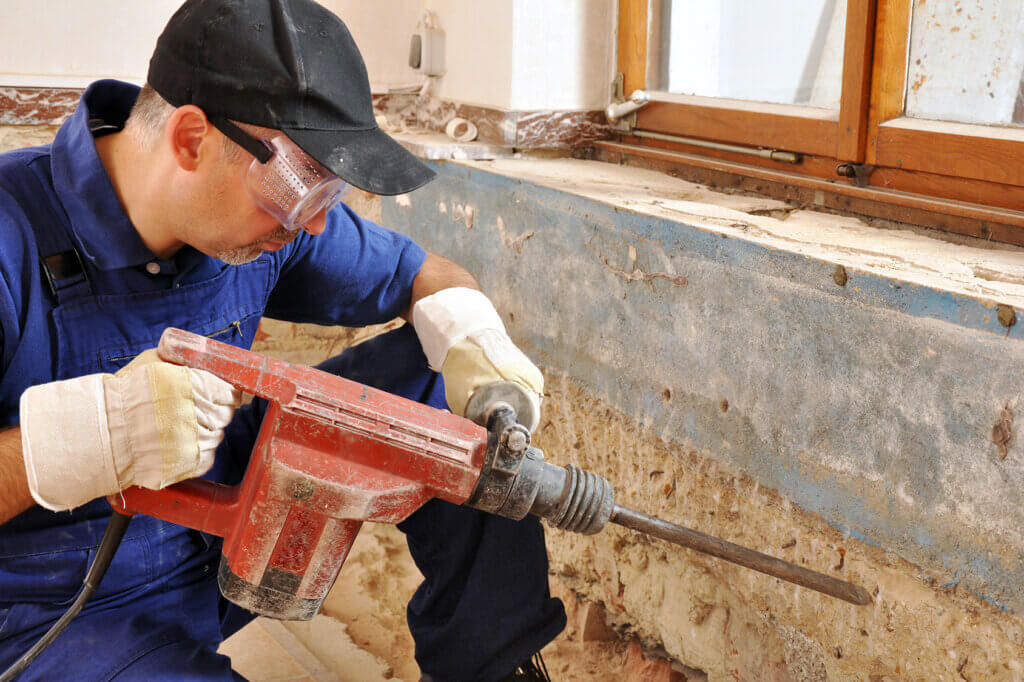
A hammer drill combines the back-and-forth action of a percussion drill with the rotation of a drill. The applications of hammer drills and percussion drills are therefore similar: both machines drill holes in harder materials. That is why beginners often ask themselves how the two tools differ from each other and which tool they need for the job at hand.
The difference between a hammer drill and a percussion drill is as follows
The biggest difference between a hammer drill and a percussion drill is the percussion mechanism. A percussion drill has two helically toothed discs that produce an impact in the axial direction while rotating against each other. The speed of rotation determines the number of blows: The higher the speed, the more effective the percussion drill. However, the machine does not have its own drive that generates the impact; the impact strength therefore depends on the force the craftsman exerts on the tool to drill. The percussion can be turned off with a switch, which allows drilling in materials such as wood, metal and plastic.
The percussion mechanism of a hammer drill, on the other hand, consists of a moving mass that strikes the drill bit with the help of an electric, pneumatic or hydraulic drive. The craftsman does not have to apply any additional force: The higher the drive force, the more effective the hammer drill. The rotation and impact rates of a rotary hammer are lower than those of a percussion drill, but the energy of each individual blow is higher. With the rotary function switched off, the rotary hammer can also be used for chiselling.
If you mainly want to drill through hard rock and concrete, go for the hammer drill. If you do not need such high impact power and also want to work on softer materials such as wood, then the percussion drill is more suitable.
Types of hammer drills and how they work
A hammer drill consists of a movable drill bit that rotates in the axial direction, a drill chuck in which the drill bit is clamped, and the impact mechanism with drive that generates the impact energy. The drill chuck is the component to which you attach the desired drill attachment; however, in order to perform the simultaneous rotating and percussive movement without loss of power, there is a small clearance between the drill and the chuck so that only the attachment rotates. The hammer drill types differ on the basis of the drive: electric, pneumatic and hydraulic.
Electric hammer drills can be used almost anywhere and are ideal for DIY and craftsmen. While their power is the lowest of all, it is perfectly sufficient for most projects in these areas. Away from power sockets, power generators or rechargeable batteries ensure ease of use.
Pneumatic hammer drills are more suitable for construction sites and mining than for home and handyman use. They work on the basis of compressed air, which is regulated with a valve. Pneumatic tools are a lot more powerful than their electric counterparts. To use them, however, you need a compressor that generates the necessary compressed air.
There are also hybrids: electric hammer drills with pneumatic percussion. These models combine the high impact force of pneumatic models with the flexibility of electric devices. In contrast to purely pneumatic rotary hammers, they are therefore also suitable for do-it-yourselfers.
The most powerful devices are hydraulic hammer drills, which drive the piston with hydraulic fluids. They are optimised for use on large machines, for example as demolition hammers on excavators. Hydraulic hammer drills are very suitable for large construction sites, industrial plants or mining, but they are not relevant for professional craftsmen or (hobby) do-it-yourselfers.
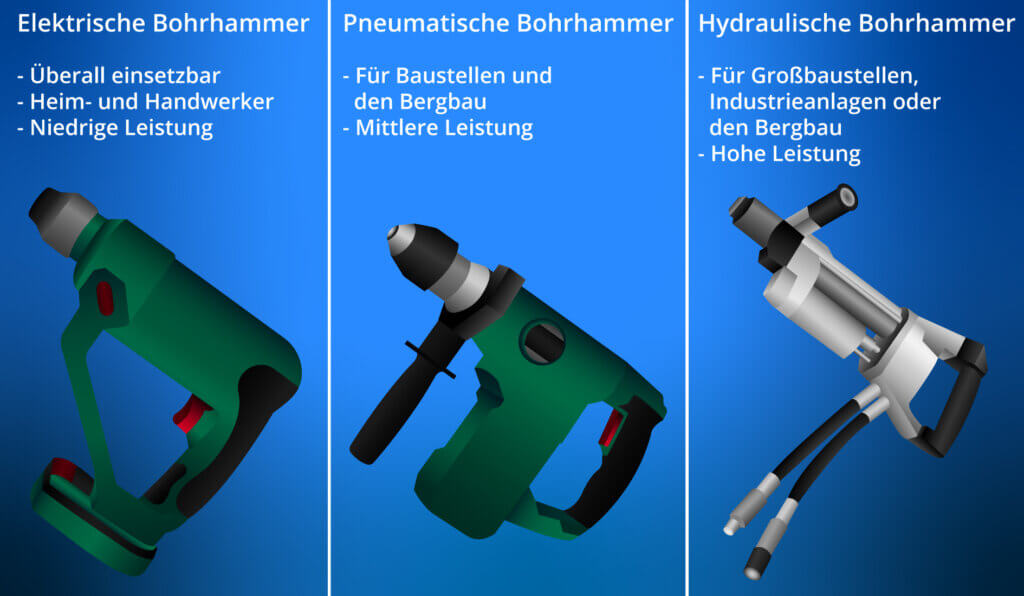
Typical attachments for rotary hammers
Depending on the field of application, different drill attachments are available. For fine chisel work, for example, a wide chisel is unsuitable.
The pointed chisel has a point tip that is either tapered to the shank or has four to six flanks. It is excellent for more intricate detail or when you want to strike deep and fast into the material.
A channel chisel has the shape of a hollow semicircle in cross-section, open at the top. It is suitable for creating joints in masonry, for example for cable ducts.
Flat chisels are universal chisels: Depending on how wide the tip is, different tasks can be performed by the special chisels. The most common use of a flat chisel, however, is to knock off old tiles.
The last important chisel is the splitting chisel with a wide tip for splitting different materials. Due to its high splitting power, it is suitable even for the hardest materials.
The classic drill bit is the concrete drill bit. It is available in several lengths and diameters and with two or four flanks.
A core bit, also called a core hole drill, drills large holes in concrete and stone. Unlike other drill bits, which pulverise the removed material in the drill hole, a cylindrical drill core is produced when working with a drill bit.
So-called multi-purpose drills allow you to drill through even reinforced concrete. Although this is done more slowly than with tools that are each optimised for either steel or concrete, their strength lies in their multifunctionality.
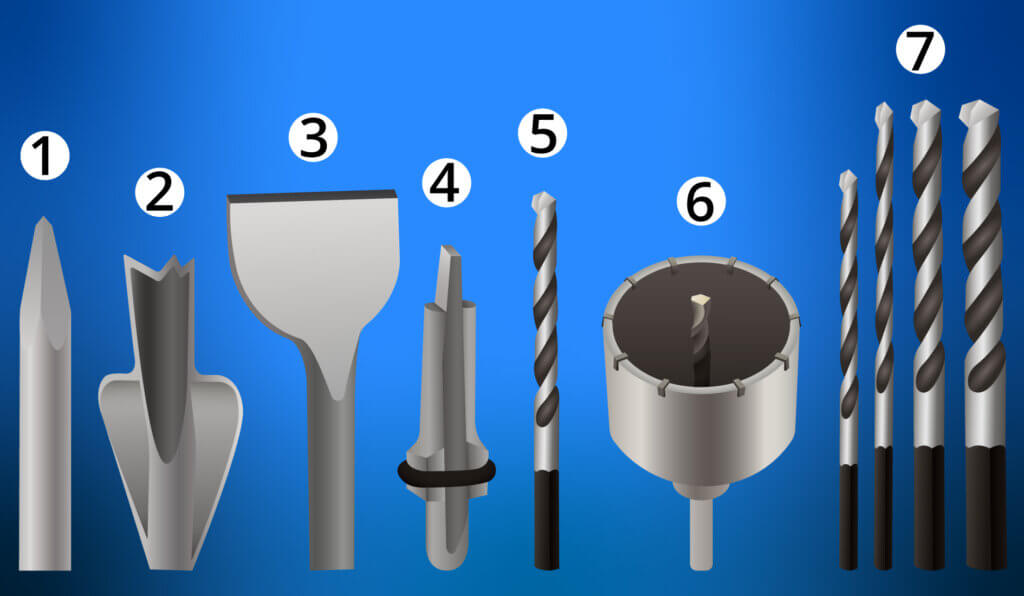
What you should look for when buying
When you look at the product description of an (electric) hammer drill, you are confronted with technical terms and measurements that you may not be able to classify, for example the impact force in joules. Finding the right tool with the features you really need among the large number of hammer drills can be a challenge. The following criteria will help you make the right purchase decision.
The power
The drive generates the power that the hammer drill needs to implement the characteristic rotary and percussive motion. The power of the drive in watts is therefore an important criterion for determining the efficiency of the entire device. You will often find this information in product descriptions under the term “rated input”. The higher the wattage, the higher the impact force. An electric hammer drill for private use should have at least 700 watts; this is enough for most projects in the home.
The impact
Two factors play an important role in the impact: the impact strength in joules and the number of blows per second. Together they determine the effectiveness of the hammer drill.
The higher the impact strength, the better the drill hits even harder rock. However, high individual impact strengths also mean a high weight and lower impact numbers. To determine the number of impacts, manufacturers measure how often the drill impacts within one minute when idling. You can find this no-load impact number in the product description.
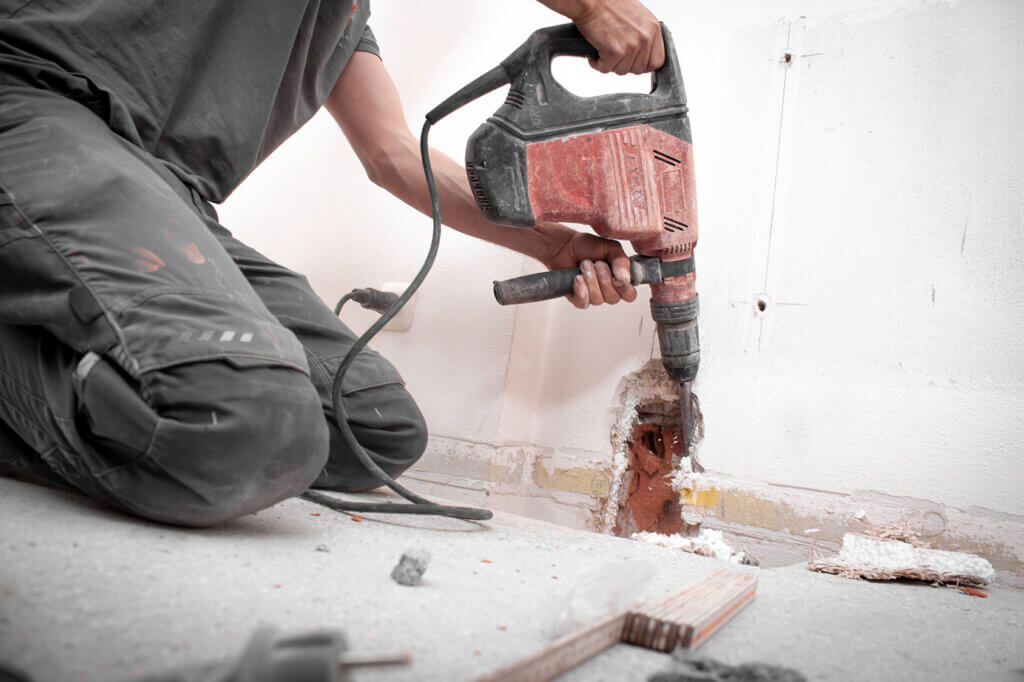
For hard concrete, a medium number of blows and a medium impact energy are recommended; for softer materials, the impact strength should be smaller and the number of blows higher. In contrast, a high impact energy with a low impact number is better for hard or rough work such as demolition and very hard concrete. Depending on the materials and the place of use, you should therefore weigh up the relationship between impact strength and number of blows.
For private use in the home, a strength of about two to four joules per blow and an idle speed of about 4,000 to 5,000 blows per minute are recommended.
The idle speed
Another information you will often find in product descriptions is the idle speed. It indicates how often the drill chuck rotates in one minute without drilling attachments. While a high speed is recommended in most cases, a very high speed with a low impact force means that the hammer drill cannot drill through softer concrete. With some models, the number can be adjusted steplessly or by regulator and thus adapted to the material requirements.
The weight
Depending on the type of drive, rotary hammers can be very heavy; even the compact electric rotary hammers for domestic use weigh between two and six kilograms on average. Heavier models tend to be more powerful – but bear in mind that you will need to hold the tool in your hands throughout use. A powerful hammer drill is of no use if you cannot operate it because of its weight. A lighter model is more advantageous, especially for long-duration work. It is therefore advisable to weigh up the weight against the performance and, if in doubt, choose a lighter hammer drill with less power.
Handling and comfort
If you want to use the hammer drill as a chisel, you should be able to easily switch off the rotary function. Some models also have an impact stop, which makes them combination tools: a switched-off impact mechanism allows you to drill into softer materials such as wood, as the material does not break in the mode.
A clockwise and anti-clockwise rotation come in handy when the drill head gets stuck in concrete. In this case, you can have the drill bit rotate in the other direction, which makes it easier to free it.
For the necessary comfort, the hammer drill should not only have an appropriate weight, but also lie well in the hand. Soft rubber handles contribute to this. Models with high impact force and rotational speed often vibrate during operation. To protect the arms from these vibrations, some powerful models have vibration damping in the handle.
Important accessories
In addition to various drill attachments, there are other accessories that are useful for working with hammer drills: protective equipment for your safety as well as equipment for the hammer drill itself.
For your safety
Probably the most important protective device you need when working with a hammer drill is hearing protection. Most hammer drills reach volumes of more than 90 decibels, and very powerful devices even exceed 100 decibels. Prolonged use without protection would permanently damage your ears, as this is already possible at a volume of more than 85 decibels.
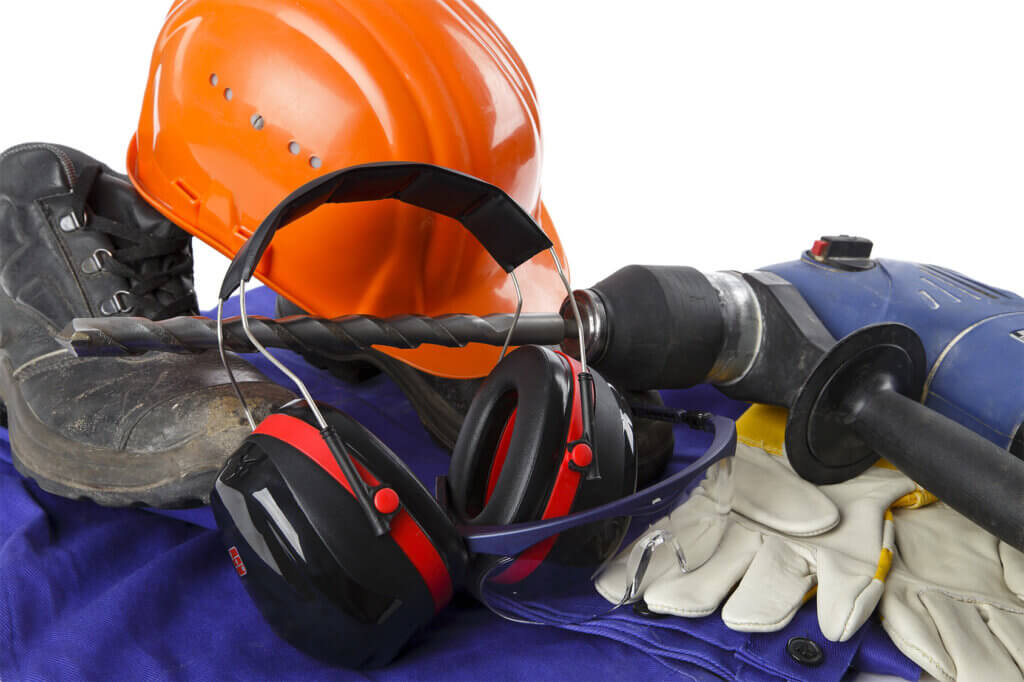
When you drill or chisel with a hammer drill, debris, dirt and dust are produced. With safety goggles, you can prevent such particles from getting into your eyes and causing injuries. This can happen quickly, especially when drilling overhead.
Gloves are not absolutely necessary, but they provide a firmer grip and also protect you from injury, for example if you come into contact with the still-hot drill shortly after working.
For the hammer drill
Modern hammer drills are equipped with a special quick-action drill chuck so that you can change the different drill attachments quickly and without a drill chuck key. The tool-free change is based on special grooves in the heads of the insert tools, which not only enable quick fixing but also ensure better power transmission between the machine and the attachment. Conventional drill bits are not compatible with these quick-change systems due to their round and smooth shanks:
- SDS-plus with a shank diameter of 10 millimetres,
- SDS-max with a shank diameter of 18 millimetres, and
- SDS-quick with a shaft diameter of 6.8 millimetres.
What does “SDS” mean?”Today’s SDS quick-action system, or more precisely SDS-plus, is a Bosch development based on Hilti’s insertion system. Originally, “SDS” stood for “plug-in rotary seat”, which was replaced by “clamping by system” and resulted in the current term “Special Direct System”. After Bosch’s patent expired, SDS-plus became the standard for hammer drills independent of manufacturers.
To attach drill bits with a round shank to a hammer drill, you need an interchangeable drill chuck, which you put onto the drill shaft by means of a lock and coupling. The larger selection of drill attachments also allows you to use the drill for materials such as wood or metal. In this way, you combine several tools in one housing.
Another practical feature is a depth stop, which ensures that you do not exceed the preset drilling depth. With a depth stop, your holes have exactly the depth you need.
Chisel grease is important for the maintenance and care of your hammer drill, as the area between the shaft and the chuck should always be well greased. If your machine is equipped with an interchangeable chuck, you should also apply the chisel grease to the coupling to the pick-up shaft.
The right care
In order to enjoy your hammer drill for a long time, you should clean and maintain it regularly. As the drill bit moves axially back and forth in the SDS chuck, friction occurs between the shaft and the chuck. If this area is not sufficiently greased, wear will occur, which is why it should be checked before use. The clutch on a tool with an interchangeable chuck also wears out, making the drill less accurate. For drilling in metal, however, a certain accuracy is essential, which is why this area must also always be sufficiently greased.
You should not neglect regular maintenance of the motor and its ventilation. Drilling in concrete causes a lot of dust; electric tools, including hammer drills, are sensitive to this. Therefore, it is advisable to clean the outside of the device with compressed air. Furthermore, it makes sense to clean the inside of the casing. However, you should leave such cleaning to a specialist, as opening the housing on your own will result in the loss of warranty claims.